Diseño y desarrollo de productos
Al reunir una cartera completa de diseño, creación de prototipos, simulación, pruebas y desarrollo bajo un mismo techo, nuestro ciclo de desarrollo completamente fusionado nos permite ofrecer un paquete de control de diseño optimizado en línea con el diseño y desarrollo de productos para componentes y conjuntos.
Nuestros ingenieros de diseño y desarrollo impulsan su idea desde el concepto hasta su finalización, incluyendo, en el proceso, los métodos y tecnologías más sofisticados de la industria de productos y dispositivos. En AnsixTech, realizamos diligentemente revisiones, identificación de peligros y análisis de riesgos a lo largo de nuestro proceso documentado.
El diseño y desarrollo de productos es un proceso complejo y crítico que implica la transformación del concepto al producto real. En este proceso, es necesario considerar de manera integral múltiples factores, como la demanda del mercado, la viabilidad técnica y la experiencia del usuario, para garantizar que el producto final pueda satisfacer las necesidades de los usuarios y ser competitivo.
En primer lugar, la investigación de mercado es una parte importante del diseño y desarrollo de productos. A través de la investigación de mercado, puede comprender las necesidades y preferencias de los usuarios, así como las tendencias del mercado y los competidores. Esto ayuda a determinar el posicionamiento y las características del producto y proporciona orientación para el diseño y desarrollo posteriores. La investigación de mercado se puede realizar mediante cuestionarios, entrevistas, observaciones, etc. Los datos y la información recopilados pueden ayudar al equipo de diseño a comprender mejor las necesidades de los usuarios y proporcionar una base para el diseño del producto.
En segundo lugar, el análisis de requisitos es un paso clave en el diseño y desarrollo de productos. En esta etapa, es necesario comprender en detalle las necesidades de los usuarios y traducirlas en funciones y características del producto. A través de la comunicación y la retroalimentación con los usuarios, el diseño del producto se puede optimizar continuamente para garantizar que el producto realmente pueda resolver los problemas de los usuarios. El análisis de requisitos se puede realizar a través de entrevistas de usuarios, historias de usuarios, análisis de casos de uso, etc. A través de una comunicación profunda con los usuarios, el equipo de diseño puede comprender mejor las necesidades de los usuarios y brindar orientación para el diseño del producto.
Luego viene el diseño conceptual, que es el proceso de transformar el concepto de un producto en un diseño concreto. En esta etapa, debe considerar la funcionalidad, el diseño, la interfaz de usuario, etc. del producto. Al dibujar bocetos, hacer modelos, etc., puede materializar ideas de diseño y discutir y brindar comentarios con los miembros del equipo y los usuarios. El diseño conceptual se puede llevar a cabo mediante dibujo a mano, diseño CAD, modelado 3D, etc. Mediante iteración y optimización continuas, finalmente se determina el plan de diseño del producto.
Luego está la creación de prototipos, al realizar prototipos del producto se puede verificar la viabilidad y la experiencia del usuario del diseño. Un prototipo puede ser un modelo físico, un modelo virtual o un modelo de interfaz interactiva. A través de pruebas y comentarios con los usuarios, se pueden descubrir y solucionar problemas, y se puede optimizar aún más el diseño del producto. La creación de prototipos se puede realizar mediante impresión 3D, tecnología de realidad virtual, fabricación de prototipos, etc. A través de la interacción y las pruebas con los usuarios, el equipo de diseño puede comprender mejor las necesidades de los usuarios y brindar comentarios y oportunidades de mejora para el diseño del producto.
Durante la fase de prueba, es necesario probar la funcionalidad, el rendimiento, la experiencia del usuario, etc. del producto. A través de las pruebas, se pueden descubrir problemas y deficiencias del producto y se pueden realizar mejoras y reparaciones. El objetivo de esta etapa es asegurar la calidad y estabilidad del producto para brindar una buena experiencia de usuario. Las pruebas se pueden realizar mediante pruebas de software, pruebas de hardware, pruebas de experiencia del usuario, etc. A través de pruebas y comentarios continuos, el equipo de diseño puede mejorar continuamente el diseño y la funcionalidad del producto, así como mejorar la calidad del producto y la satisfacción del usuario.
El diseño y desarrollo de productos es un proceso integral que requiere una consideración integral de la demanda del mercado, la viabilidad técnica, la experiencia del usuario y otros factores. A través de la investigación de mercado, el análisis de la demanda, el diseño conceptual, la creación de prototipos, las pruebas, la fabricación y el marketing, el concepto de un producto se puede transformar en un producto realmente utilizable que satisfaga las necesidades del usuario y sea competitivo. En este proceso, el equipo de diseño necesita cooperar con múltiples departamentos y equipos, como el departamento de marketing, ingenieros y fabricantes, para mejorar la calidad del producto y la satisfacción del usuario mediante la innovación y la mejora continua.
Proceso de control de diseño de productos y dispositivos
La fase inicial desde la que comienza el Control de diseño es el desarrollo y aprobación de los insumos de diseño, que consiste en el diseño del dispositivo y los procesos de fabricación que se trasladarán a la fase de producción.
El control del diseño es una estrategia holística y no termina con compartir el diseño en la fase de producción una vez finalizado. También mueve los procesos de fabricación de acuerdo con los cambios en la etapa de diseño o incluso la retroalimentación de posproducción. Es un proceso continuo desarrollar un producto utilizable para un usuario y, para el producto mejorado, considerar cambios revolucionarios en los patrones de uso y diagnosticar productos fallidos.
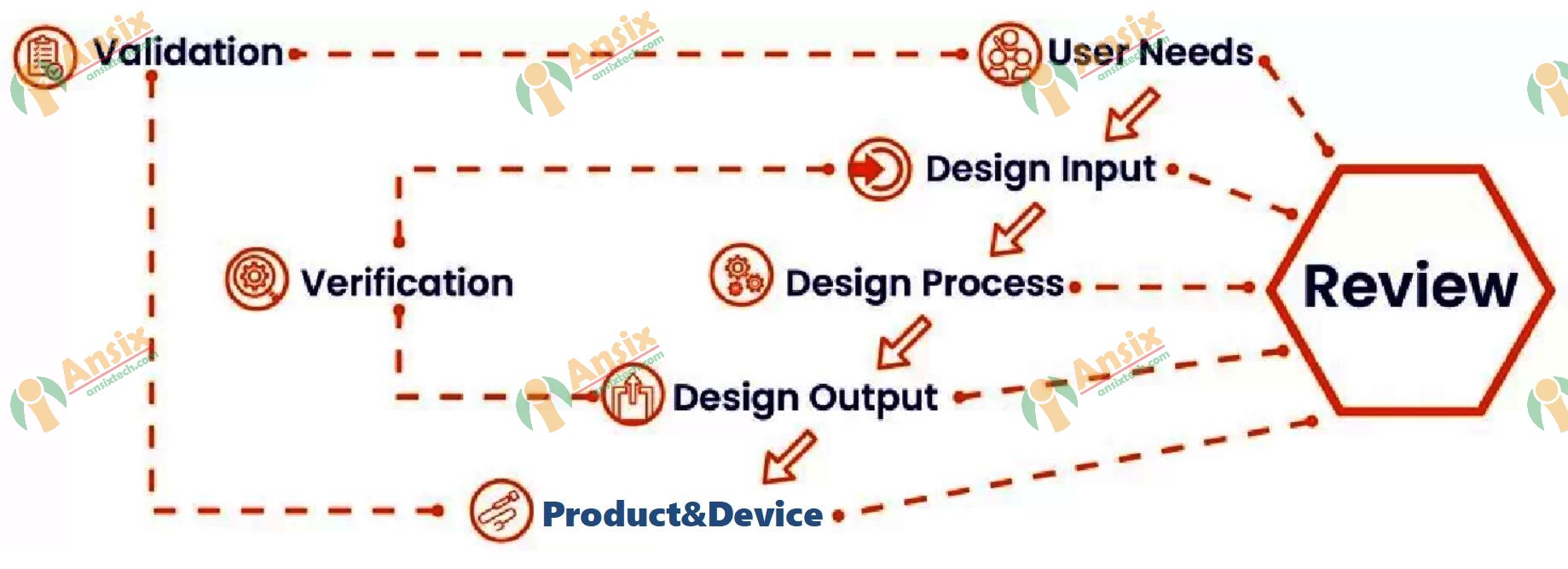
El proceso de control del diseño del producto se refiere al proceso de garantizar la calidad y el progreso del diseño del producto a través de una serie de medidas y métodos de control durante el proceso de diseño y desarrollo del producto. Los siguientes son los pasos generales del proceso de control del diseño del producto:
Establecer objetivos y requisitos de diseño: antes de comenzar el diseño del producto, es necesario aclarar los objetivos y requisitos de diseño del producto. Esto incluye la función del producto, el rendimiento, la apariencia, el costo, el proceso de producción y otros requisitos. Estos objetivos y requisitos formarán la base para el control del diseño.
Desarrollar un plan de diseño: Desarrolle un plan de diseño detallado basado en los objetivos y requisitos del diseño. El plan de diseño incluye el cronograma de diseño, las etapas y tareas de diseño, la asignación de recursos de diseño, etc. El plan de diseño ayudará al equipo a aclarar el progreso y las responsabilidades del diseño y garantizará que el diseño avance según lo planeado.
Revisión del diseño: en el proceso de diseño, la revisión del diseño es una medida de control muy importante. Las revisiones de diseño se pueden realizar en cada etapa de diseño o en puntos importantes de decisión de diseño. A través de la revisión, se puede verificar la racionalidad, el cumplimiento y la viabilidad del diseño, se pueden descubrir y resolver problemas y se puede garantizar la calidad y la implementabilidad del diseño.
Verificación y verificación del diseño: una vez completado el diseño, es necesaria la verificación y verificación del diseño. La verificación del diseño consiste en verificar si la función y el rendimiento del diseño cumplen con los requisitos mediante simulación, experimento o cálculo. La verificación del diseño se puede llevar a cabo mediante pruebas de prototipos, simulación, verificación experimental, etc. Los resultados de la verificación del diseño determinarán si se necesitan modificaciones y optimizaciones del diseño.
Control de cambios de diseño: Durante el proceso de diseño, pueden ocurrir cambios en la demanda, problemas técnicos, cambios de mercado, etc., que requieran cambios de diseño. El control de cambios de diseño es el proceso de garantizar la racionalidad y controlabilidad de los cambios de diseño. Los cambios de diseño deben revisarse y aprobarse para garantizar que no tengan un impacto incontrolable en la calidad, el cronograma y el costo del producto.
Control de documentos de diseño: durante el proceso de diseño, es necesario generar una gran cantidad de documentos de diseño, incluidas especificaciones de diseño, informes de diseño, dibujos de diseño, etc. El control de documentos de diseño es el proceso de garantizar la precisión, integridad y trazabilidad de los documentos de diseño. . Los documentos de diseño deben controlarse, revisarse y archivarse para su posterior uso en diseño y producción.
Control de calidad del diseño: durante el proceso de diseño, se debe realizar un control de calidad del diseño para garantizar que la calidad del diseño cumpla con los requisitos. El control de calidad del diseño incluye el control de la racionalidad del diseño, la confiabilidad, la capacidad de fabricación, la mantenibilidad y otros aspectos. A través del control de calidad del diseño, se pueden reducir los errores y defectos de diseño y mejorar la calidad y confiabilidad del producto.
Control del progreso del diseño: Durante el proceso de diseño, se requiere control del progreso del diseño para garantizar que el diseño avance según lo planeado. El control del progreso del diseño incluye la descomposición de las tareas de diseño, el seguimiento y ajuste del progreso, la asignación de recursos, etc. A través del control del progreso del diseño, los retrasos en el progreso del diseño se pueden descubrir y resolver de manera oportuna para garantizar que el diseño se complete a tiempo.
En la aplicación real, se pueden realizar ajustes y complementos en función de las condiciones organizativas y del proyecto específico. El objetivo del control del diseño es garantizar la calidad y el progreso del diseño, reducir los riesgos del diseño y mejorar la competitividad del producto y la tasa de éxito en el mercado.
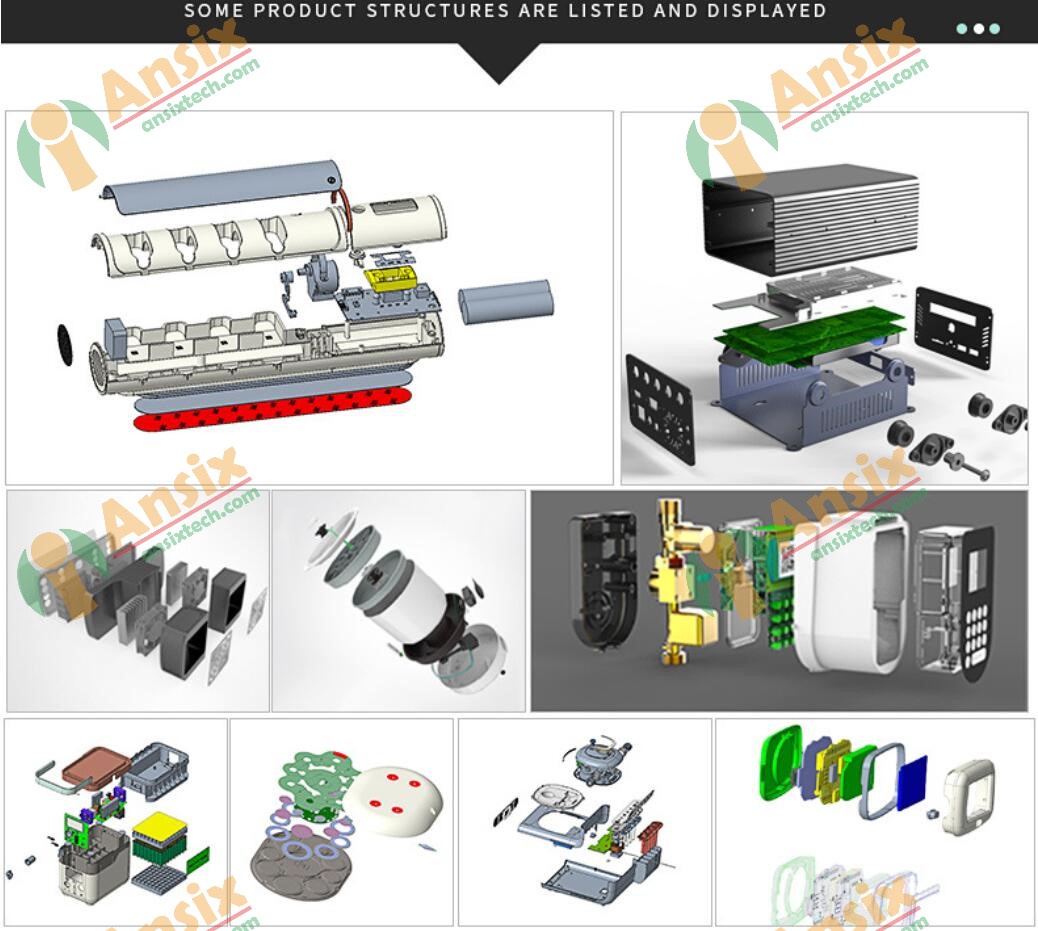
Gestión de la cadena de suministro de materias primas.
En AnsixTech, ponemos gran énfasis en la gestión de la cadena de suministro de materias primas y en la precisión y confiabilidad del tiempo de entrega. Estas son algunas de nuestras prácticas y compromisos:
Selección y evaluación de proveedores: Establecemos relaciones de cooperación a largo plazo con proveedores confiables y evaluamos periódicamente su tasa de entrega a tiempo, la calidad del producto y el nivel de servicio. Elegimos proveedores que puedan satisfacer nuestras necesidades y tengan capacidades de suministro estables.
Previsión y planificación: Predecimos la cantidad y el tiempo de materia prima necesaria a través de estudios de mercado y previsión de la demanda. Formulamos planes de compras razonables y nos comunicamos con los proveedores de manera oportuna para garantizar que el suministro de materias primas pueda satisfacer nuestras necesidades de producción.
Gestión de inventario: Realizamos una gestión de inventario precisa para evitar niveles de inventario excesivamente altos o bajos. Realizamos recuentos y análisis de inventario periódicos para garantizar la precisión y puntualidad del inventario.
Colaboración en la cadena de suministro: Mantenemos una estrecha comunicación y colaboración con nuestros proveedores. Comunicamos los cambios en la demanda y los tiempos de entrega a nuestros proveedores de manera oportuna para garantizar la fluidez y coordinación de la cadena de suministro.
Cadena de suministro diversificada: hemos establecido relaciones de cooperación con múltiples proveedores para reducir los riesgos de la cadena de suministro. Si un proveedor no puede satisfacer la demanda, podemos cambiar rápidamente a otros proveedores para garantizar que el suministro de materias primas no se vea afectado.
Seguimiento y Monitoreo: Realizamos un seguimiento del estado de entrega y el progreso de las materias primas y resolvemos rápidamente cualquier problema que pueda causar retrasos. Utilizamos sistemas de gestión de la cadena de suministro y otras herramientas para monitorear el funcionamiento de nuestra cadena de suministro de modo que se puedan descubrir y resolver problemas potenciales de manera oportuna.
Compromiso de tiempo de entrega: Nos comprometemos a entregar los productos rápidamente de acuerdo con los requisitos de tiempo de entrega del cliente. Formulamos planes de producción y arreglos logísticos razonables basados en las necesidades del cliente y el tiempo de entrega para garantizar que los productos puedan entregarse a los clientes a tiempo.
Para materias primas generales, podemos pedir a los proveedores que entreguen las materias primas a nuestra fábrica en un plazo de 2 horas.
A través de las medidas de gestión de la cadena de suministro y los compromisos de tiempo de entrega anteriores, nos esforzamos por garantizar el suministro oportuno de materias primas y la entrega rápida de productos. Mejoramos continuamente la eficiencia y confiabilidad de la gestión de la cadena de suministro para satisfacer las necesidades y expectativas de los clientes.
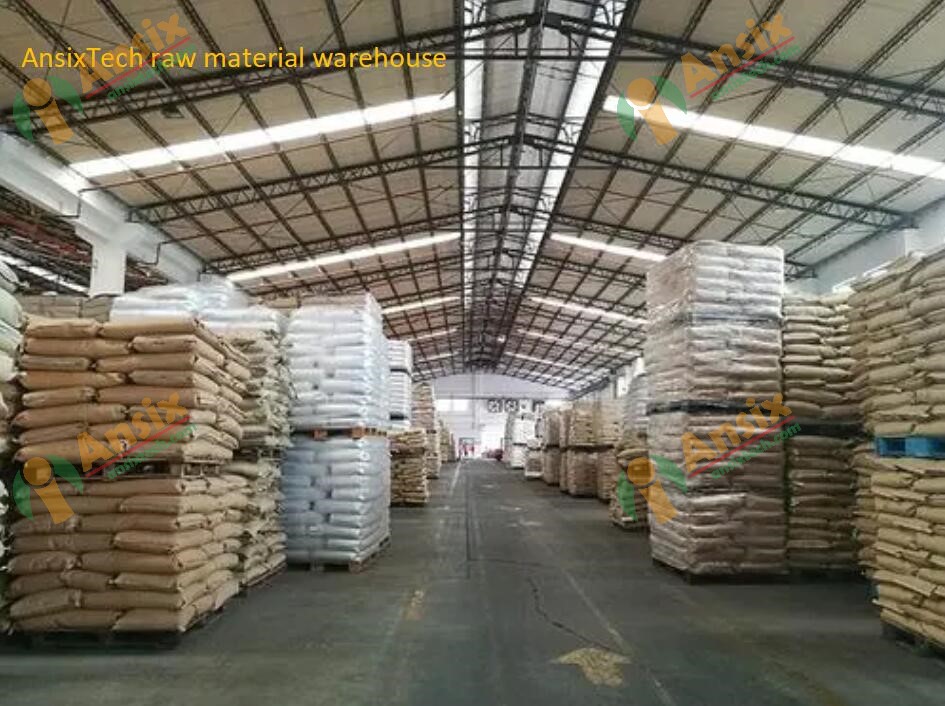
Pruebas – Verificación y Validación
Cada producto y dispositivo debe cumplir con los objetivos de funcionalidad, usabilidad y confiabilidad para obtener una participación exitosa en el mercado. Aparte de esto, los usuarios finales también buscan la eficacia y seguridad de los dispositivos que utilizan para gestionar un problema o situación particular, que a veces son críticos para la vida. Es por eso que las pruebas iterativas para verificar y validar estos dispositivos médicos se vuelven obligatorias.
Los productos y dispositivos pueden consistir en diversas formas y tamaños tecnológicos y diferentes niveles de complejidad. La acción de verificación y validación (V&V) está guiada por el entorno regulatorio y debe seguir estándares internacionales.
Nuestras actividades estandarizadas de V&V pueden simplificar el proceso de fabricación y mejorar el proceso de aprobación. Además, las pruebas automáticas, las técnicas de diagnóstico y las herramientas de recopilación de datos pueden mejorar el procedimiento de V&V.
La complejidad de cualquier proceso de prueba depende de las tecnologías utilizadas y de los mercados geográficos de destino. La estrategia de prueba debe ocultar al menos seis parámetros que se mencionan a continuación:
Geografías objetivo y estándares asociados
Tiempo para comercializar la demanda
Una medida a observar con la versión.
Laboratorios de pruebas: laboratorios internos o externos
Definición de la disposición de las pruebas.
Presentando el resultado de la prueba
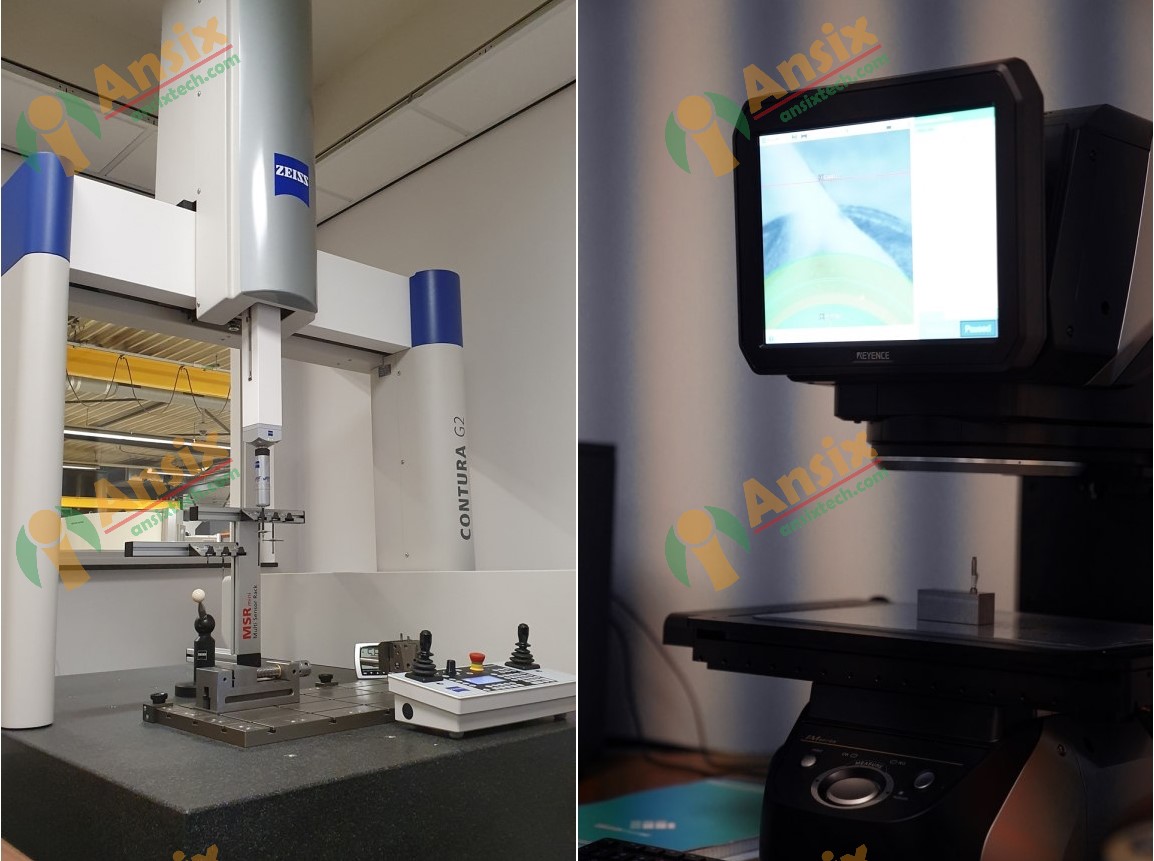
Beneficios de los servicios de diseño y desarrollo
AnsixTech es una extensión de su equipo de desarrollo y puede ayudarlo desde el inicio de su proyecto. Nos asociamos con nuestros clientes brindándoles ingeniería de primer nivel de principio a fin, desarrollando productos diseñados con valor. Contamos con todos los recursos esenciales para integrar nuestras actividades en los métodos de desarrollo de productos y cadena de suministro de nuestros clientes, de modo que nuestros clientes puedan obtener beneficios sustanciales.
Protección de propiedad intelectual:
Seguridad de la propiedad intelectual de los productos. Además de los acuerdos de no exposición, AnsixTech mantiene sistemas sólidos para proteger los datos de los clientes. Acceso sólo para el departamento de diseño con un sistema de servidor independiente.
Desarrollo de iteraciones:
Equipos dedicados para extrusiones rápidas y moldeo por inyección. Los accesorios y el equipo de montaje están listos para las iteraciones.
Un equipo de ingenieros y administradores de programas está listo para ayudarlo con las demandas de iteración y diseño de sus productos y dispositivos.
Reducir los costos de fabricación
Nuestras capacidades cubren una amplia gama de productos y dispositivos. Los miembros de nuestro equipo tienen una amplia experiencia en el diseño, desarrollo y fabricación de productos y dispositivos, lo que nos brinda una experiencia de primera mano con las necesidades de desarrollo de productos de la industria. Estamos bien versados en la última tecnología, incluida la usabilidad, el software y los equipos.
Con una amplia experiencia tanto en las fases de diseño inicial como en la fabricación final, el equipo de AnsixTech puede diseñar productos y dispositivos de alto rendimiento que también se pueden fabricar de manera eficiente y rentable. Nuestra experiencia en diseño para la capacidad de fabricación puede reducir la complejidad, reduciendo los costos y los problemas de calidad, al tiempo que garantiza operaciones de fabricación eficientes y a largo plazo.
Como extensión del departamento de I+D de su empresa, desarrollamos rápidamente un plan detallado que minimiza los pasos pero optimiza el rendimiento del material.
Acelere el tiempo de comercialización y minimice el riesgo
Nuestro modelo de negocio desde el concepto hasta el suministro acelera el tiempo de comercialización y reduce los riesgos para nuestros clientes. Podemos llevarlo allí con cumplimiento de ISO y QSR, habilidades de vanguardia, costos competitivos y una red establecida de conexiones globales, incluido el Lejano Oriente.
Siempre tenemos en mente su línea de meta. Respondemos con prontitud a sus demandas y podemos ajustar la planificación y la ejecución rápidamente para adaptarnos a los cambios que puedan surgir. Nuestro conocimiento de las necesidades regulatorias y de todo el proceso de comercialización brinda a nuestros clientes la confianza de que sus productos se lanzarán a tiempo.
Fortalecer la propiedad intelectual y adquirir experiencia tecnológica
Podemos ayudarlo a fortalecer su cartera de propiedad intelectual o crear una matriz de arte existente para especificar oportunidades y puntos débiles. Nuestra experiencia en la industria proporciona una revisión exhaustiva y podemos ofrecer distribución de los productos de su empresa en todos los mercados de productos y dispositivos.
Además, proporcionamos
Control de diseño.
Seguimiento de la documentación relacionada con el cumplimiento
Presentaciones regulatorias.
Abastecimiento nacional y offshore de elementos y subconjuntos.
Estudio de caso de diseño y desarrollo de productos y dispositivos
Un desafío en nuestra industria es que las empresas subcontraten el desarrollo completo de sus productos y dispositivos. Del mismo modo, las empresas emergentes a menudo construyen una cadena de suministro fragmentada y riesgosa desde el inicio del diseño.
Las empresas pueden elegir productos y componentes de dispositivos críticos de empresas que necesitan más viabilidad financiera u operativa para suministrar piezas de forma competitiva a largo plazo. Esto puede perjudicar la capacidad de una empresa para realizar adquisiciones en el futuro o afectar su valoración al vender.
AnsixTech ayuda a los clientes a optimizar su cadena de suministro desde el principio.
Seleccione entre una variedad de servicios internos
Diseñe su cadena de suministro desde cero con el equipo de ingenieros calificados y experimentados de AnsixTech.
Desde el principio, optimizar el diseño para la fabricación y la cadena de suministro evita problemas a corto y largo plazo.
Proporcionar servicios profesionales de diseño de moldes
El diseño de moldes de inyección de plástico implica desarrollar un molde con características idénticas a la pieza que se pretende fabricar.
En AnsixTech, utilizamos tecnología de alta precisión para desarrollar moldes que capturen cada detalle del diseño de su pieza. Nuestro experimentado equipo de diseño y nuestro ingeniero de diseño de moldes de inyección consultarán con usted durante todo el proceso de diseño de moldes. Esto garantiza que entregamos una estructura de molde que es viable en términos de producción pero que también cumple con los requisitos de diseño de su pieza. Le garantizamos una experiencia de cliente sin estrés.
El molde de calidad comienza con un diseño excelente
El rendimiento de una herramienta depende en gran medida de la madurez de su diseño. Por lo tanto, los muchos años de experiencia de nuestros diseñadores son un factor decisivo con respecto a la calidad de la herramienta AnsixTech.
Colaboramos estrechamente con nuestros clientes en todos los aspectos de los programas para desarrollar los moldes mejor diseñados que sean fáciles de mantener y componentes plásticos cuya producción sea rentable.
Nuestro experto equipo de diseño interno tiene más de 25 años de experiencia en el diseño de herramientas personalizadas. Ofrecemos paquete de diseño completo:
Estudios de viabilidad y recomendaciones de diseño.
Simulación de llenado y análisis de Moldflow
Diseño de herramientas 2D y 3D (CAD, Unigraphics,(NX) y otras...)
Si es necesario, nuestros diseñadores pueden participar en una etapa muy temprana de un proyecto, para ayudarlo durante el desarrollo de la pieza, a fin de permitir un diseño de herramienta específica, ahorrando así tiempo y costos.
Equipo de diseño altamente calificado
En AnsixTech nos enorgullecemos de la experiencia de nuestro equipo altamente calificado de la Oficina de Diseño de Moldes, que trabaja en estrecha colaboración con los clientes para garantizar procesos de diseño eficientes y fluidos.
Se presta especial atención a la construcción del molde, los canales de enfriamiento y los mecanismos móviles para garantizar que se entreguen piezas de la más alta calidad desde su molde.
Todos los moldes están cuidadosamente diseñados para maximizar su vida útil y facilitar el mantenimiento.
Privacidad y confidencialidad
Para la fabricación, revisaremos cuidadosamente los dibujos de diseño de su producto y le brindaremos asesoramiento técnico si es necesario. Puedes modificarlo tú mismo o podemos ayudarte a mejorar el diseño. Sólo tienes que decirnos las dimensiones y funciones de la aplicación que deseas. Si solo tiene una plantilla, envíenos la plantilla o la imagen, podemos ayudarlo a restaurar el dibujo, luego usar la impresión 3D para crear el prototipo para su evaluación y, finalmente, usar el moldeo por inyección para fabricar el producto de plástico.
No tiene que preocuparse de que su producto o diseño se filtre o se venda. Somos un fabricante de OEM y ODM y un fabricante de moldes profesional; No vendemos productos. Solo personalizamos productos para nuestros clientes. Por supuesto, si no se siente cómodo, también podemos firmar un acuerdo de confidencialidad.
Diseños de herramientas de inyección de plástico
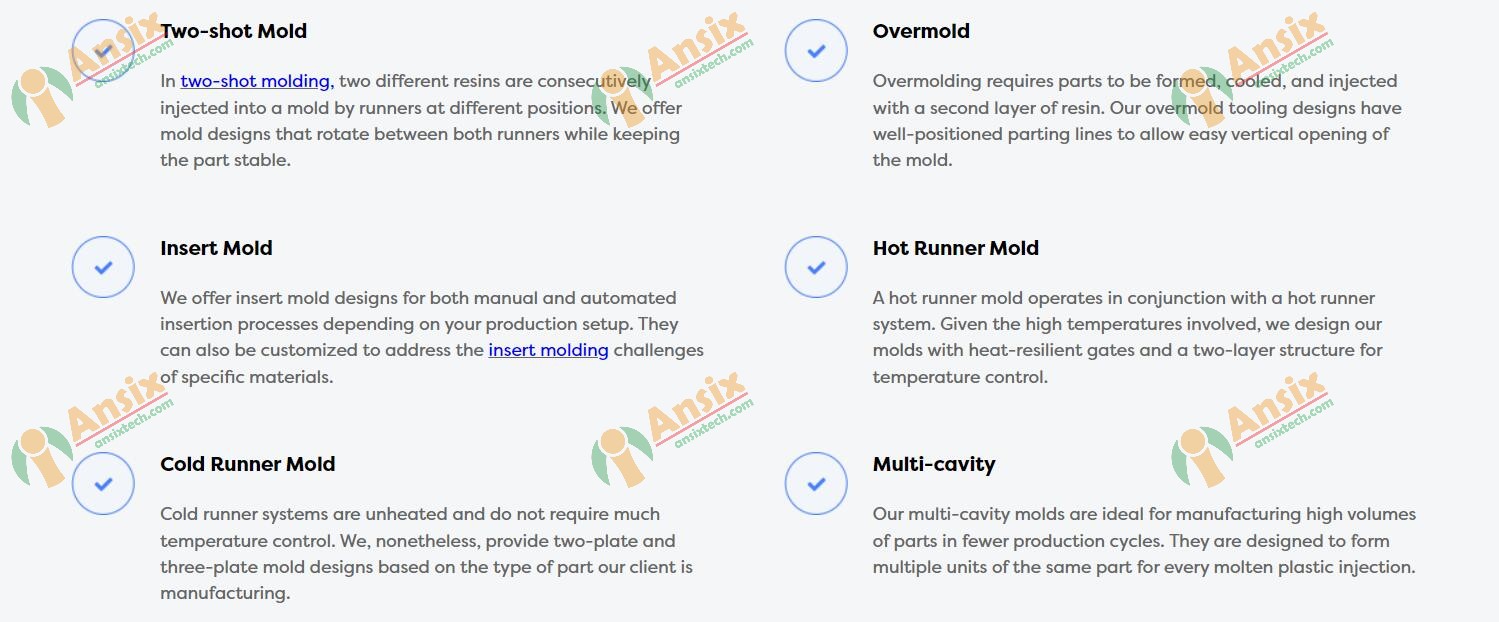
Por qué necesita un diseño de moldes de inyección
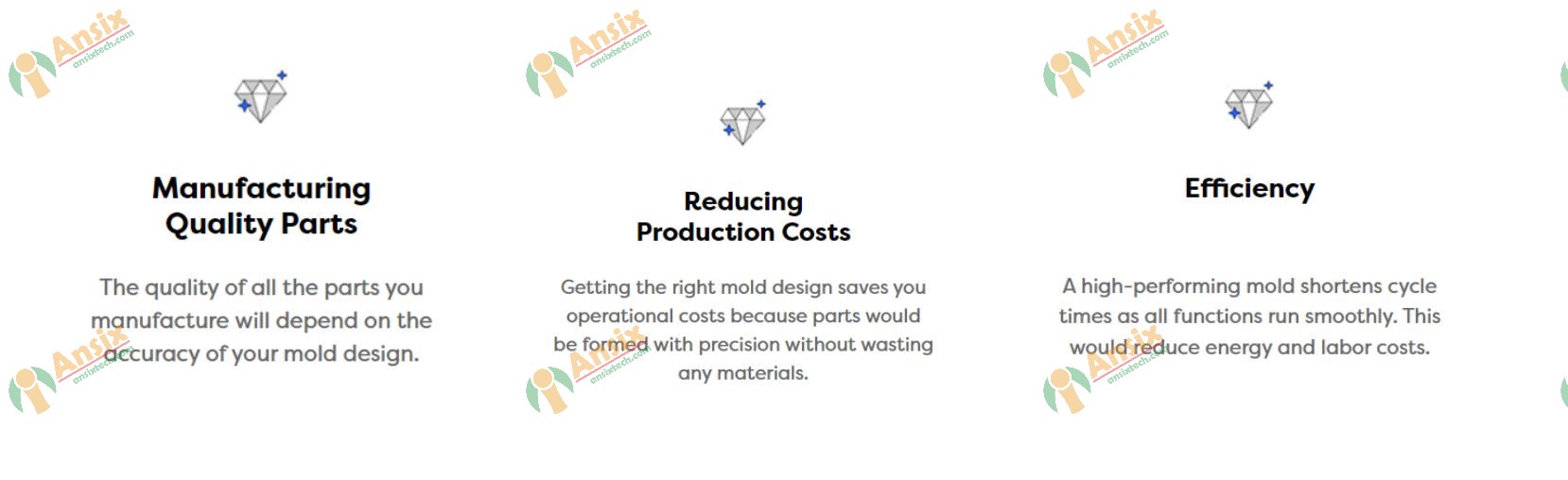
4 consideraciones para un diseño de molde de inyección perfecto
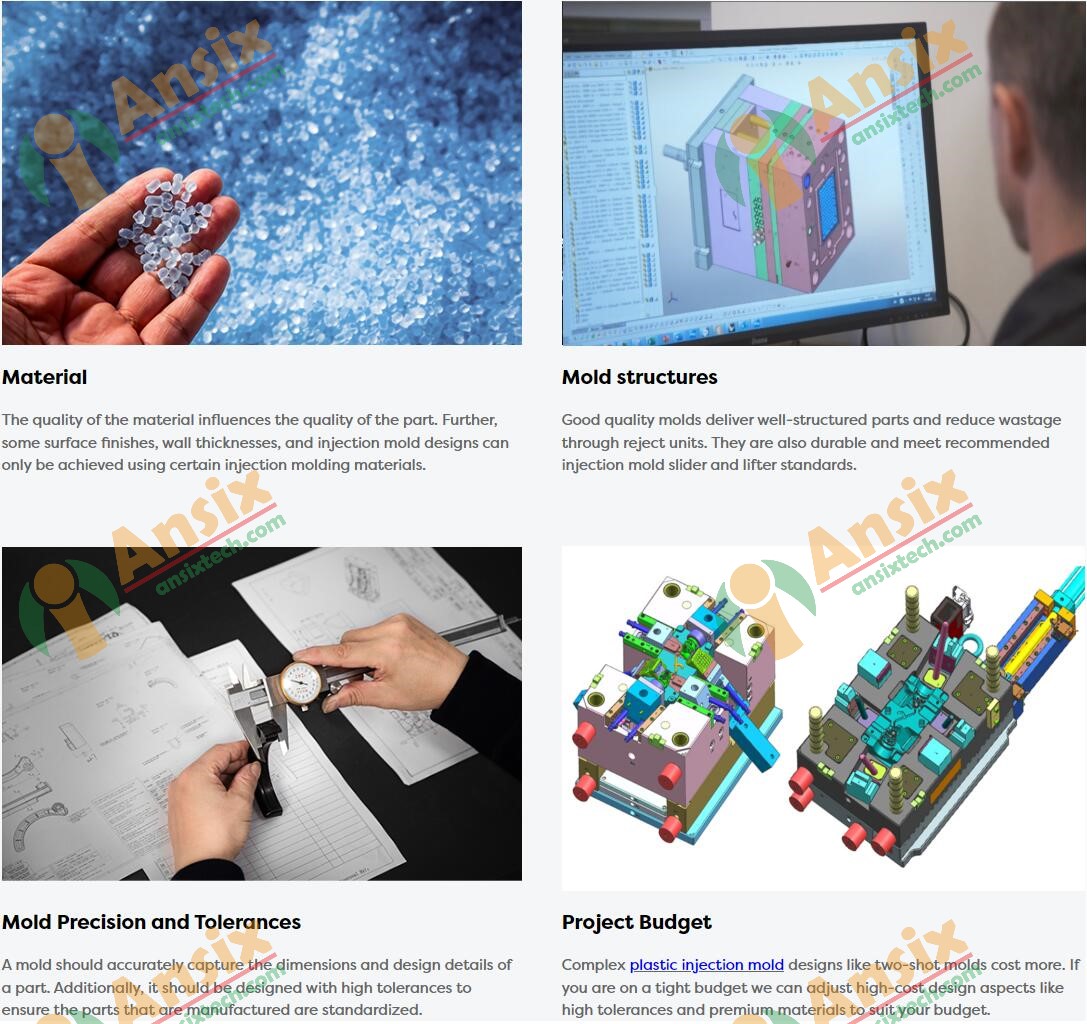
Diseños que funcionan para usted
- Como fabricante con muchos años de experiencia en la industria del moldeo por inyección de plástico, AnsixTech sabe muy bien si el diseño de un molde o de una pieza de plástico es adecuado para el proceso de fabricación. En AnsixTech, combinamos la funcionalidad del producto y la capacidad de fabricación para brindarle modificaciones en el diseño del producto, ofrecer productos que se ajusten a sus necesidades y ahorrarle tiempo y dinero.
Analisis inicial
La estructura del producto se refiere a los componentes de un producto y las relaciones entre ellos. A través del análisis de la estructura del producto, se pueden comprender la función, el rendimiento y las características del producto, y se puede proporcionar orientación para el diseño, la fabricación y el mantenimiento del producto.
El análisis de la estructura del producto se puede realizar desde los siguientes aspectos:
Componentes: el análisis de la estructura del producto primero requiere determinar los componentes del producto, es decir, en qué partes o módulos consta el producto. Desmontando y descomponiendo el producto se pueden identificar los distintos componentes del producto.
Relaciones de los componentes: el análisis de la estructura del producto también requiere determinar la relación entre varios componentes. Esto incluye los métodos de conexión, relaciones posicionales, relaciones de movimiento, etc. entre componentes. Al analizar la relación entre los componentes, se puede determinar la funcionalidad y el rendimiento de un producto.
Análisis funcional: el análisis de la estructura del producto también requiere un análisis de las funciones del producto. Es decir, determinar las funciones principales y auxiliares del producto, así como la contribución de cada componente a la función. Mediante el análisis funcional, se pueden determinar los requisitos de diseño y los indicadores de rendimiento del producto.
Análisis de desempeño: el análisis de la estructura del producto también requiere un análisis del desempeño del producto. Es decir, para determinar los principales indicadores de rendimiento del producto, como resistencia, rigidez, durabilidad, etc. A través del análisis de rendimiento, se pueden determinar los requisitos de diseño y el proceso de fabricación del producto.
Estructura general: finalmente, el análisis de la estructura del producto requiere la integración de varios componentes para formar una estructura de producto completa. Mediante un análisis estructural general, se puede evaluar el rendimiento general y la confiabilidad del producto.
A través del análisis de la estructura del producto, podemos comprender los componentes, funciones, rendimiento y características del producto y brindar orientación para el diseño, la fabricación y el mantenimiento del producto. El análisis de la estructura del producto es un vínculo importante en el proceso de desarrollo y fabricación del producto, que puede ayudar a los diseñadores e ingenieros a comprender y mejorar mejor los productos.
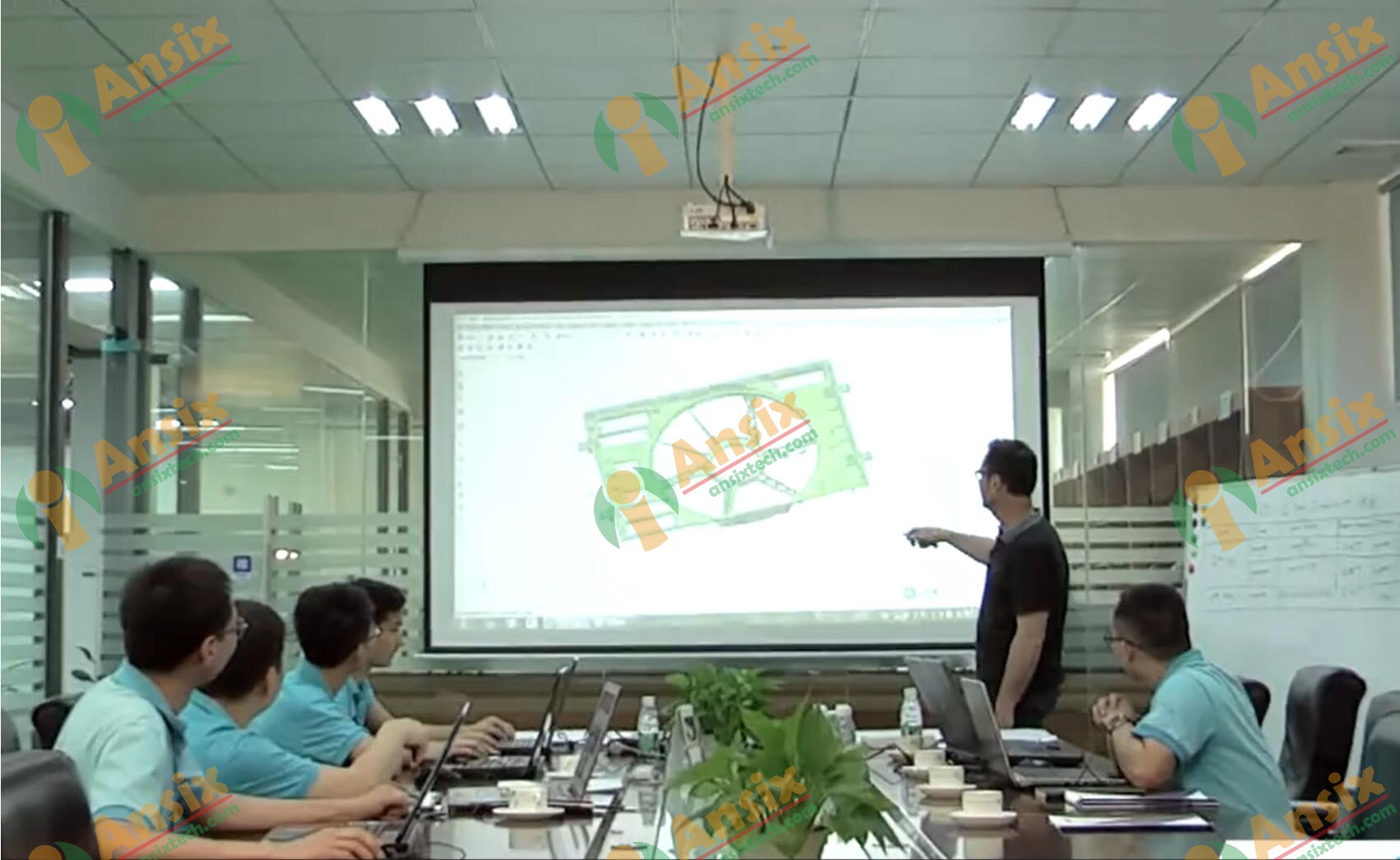
Análisis de flujo de molde
AnsixTech Tooling ofrece el servicio de análisis de flujo de molde para garantizar que los problemas de fabricación subyacentes se destaquen y detecten durante la fase de diseño como guía para mejorar el diseño. Los temas de un informe de análisis de flujo de molde generalmente incluyen:
· Modelo de análisis · Material · Sistema de canales · Sistema de enfriamiento · Configuración del proceso · Patrón de llenado, etc.
El análisis de flujo de moldes es un método que utiliza tecnología de simulación por computadora para analizar y optimizar los moldes de inyección. Mediante el análisis del flujo del molde, se pueden predecir y evaluar parámetros clave como el flujo, el llenado, el enfriamiento y la contracción durante el proceso de moldeo por inyección para ayudar a los diseñadores a optimizar el diseño del molde y mejorar la calidad del producto y la eficiencia de la producción.
Los principales pasos del análisis del flujo del molde incluyen los siguientes aspectos:
Preparación del modelo: Primero, es necesario preparar un modelo tridimensional del molde de inyección. La geometría del molde se puede dibujar utilizando un software CAD e importarse al software de análisis de flujo del molde para su posterior análisis.
Selección de material: seleccione un modelo de material de moldeo por inyección adecuado en función de los materiales utilizados en el proceso de moldeo por inyección real. Las propiedades de los materiales de moldeo por inyección tienen un impacto importante en procesos como el flujo, el llenado y el enfriamiento, por lo que la selección correcta de los modelos de materiales es la clave para el análisis del flujo del molde.
Mallado: malla el modelo del molde y discretiza la geometría del molde en unidades pequeñas. La precisión y densidad del mallado tienen un impacto importante en la precisión y eficiencia computacional del análisis de flujo del molde.
Análisis del flujo del molde: realice un análisis del flujo del molde para simular parámetros clave como el flujo, el llenado, el enfriamiento y la contracción durante el proceso de moldeo por inyección. Mediante el análisis del flujo del molde, se pueden predecir y evaluar defectos y deformaciones durante el proceso de moldeo por inyección, como disparos cortos, burbujas, deformaciones, etc.
Análisis y optimización de resultados: Realizar análisis y optimización de resultados en función de los resultados del análisis de flujo del molde. Según los resultados del análisis, se pueden ajustar parámetros como la estructura del molde, el sistema de enfriamiento y la posición de la boquilla para mejorar la calidad del producto y la eficiencia de la producción.
El análisis del flujo del molde puede ayudar a los diseñadores a comprender mejor el flujo y el comportamiento de llenado durante el proceso de moldeo por inyección, predecir y resolver problemas potenciales y mejorar la calidad del producto y la eficiencia de la producción. Mediante el análisis del flujo del molde, se puede reducir la cantidad de pruebas y costos del molde, se puede acortar el ciclo de desarrollo del producto y se puede mejorar la confiabilidad y capacidad de fabricación del diseño. Por lo tanto, el análisis de flujo de moldes tiene un importante valor de aplicación en el proceso de diseño y fabricación de moldes de inyección.
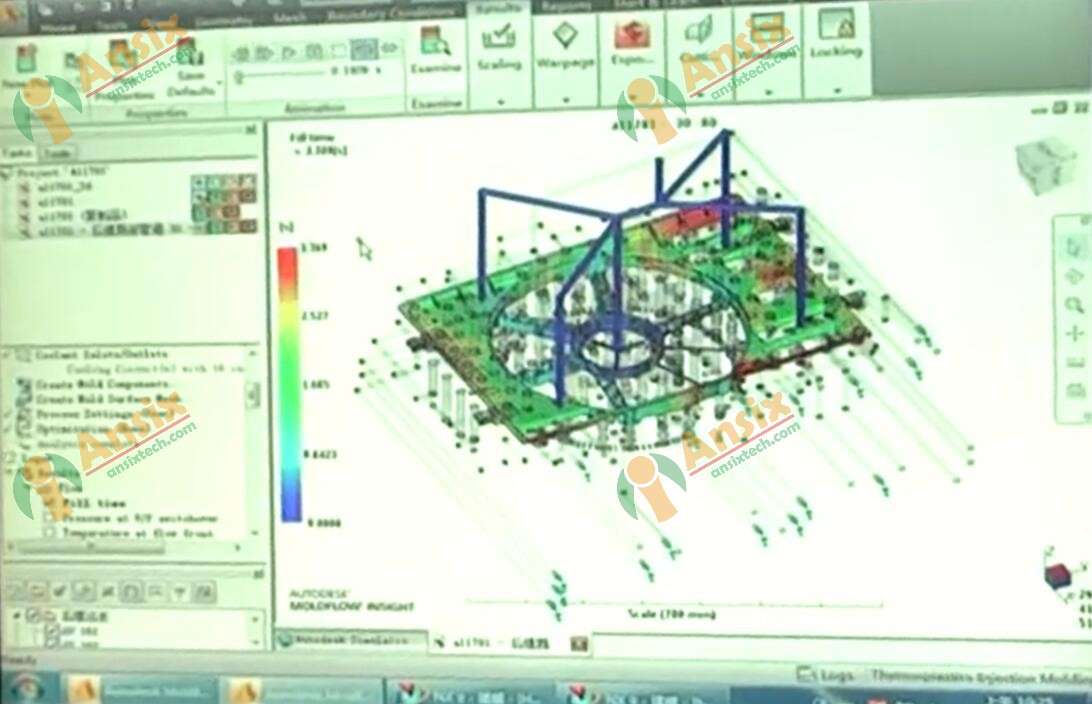
Diseño para fabricación
AnsixTech realiza un análisis de capacidad de fabricación en cada proyecto de moldeo por inyección para optimizar el diseño de piezas, minimizar los costos de herramientas y reducir el tiempo general del proyecto. El informe de análisis detallado es revisado por el diseñador principal, el fabricante de herramientas, el ingeniero de moldeo por inyección y el gerente de proyecto para garantizar que el componente solicitado sea apropiado para el moldeo por inyección.
El diseño de moldes se refiere al diseño de un molde adecuado para producir el producto según los requisitos del producto y los dibujos de diseño. El objetivo del diseño de moldes es lograr una producción de productos de alta calidad, alta eficiencia y bajo costo.
El proceso de diseño del molde incluye los siguientes pasos:
Analice los requisitos del producto: primero, debe analizar cuidadosamente los requisitos del producto y los dibujos de diseño. Comprender la forma, tamaño, material y otras características del producto, así como los requisitos de producción y el flujo del proceso del producto.
Determine el tipo de molde: determine el tipo de molde adecuado en función de las características del producto y los requisitos de producción. Los tipos de moldes comunes incluyen moldes de fundición a presión, moldes de inyección, moldes de estampado, etc. Los diferentes tipos de moldes tienen diferentes requisitos de diseño y procesos de fabricación.
Diseñar la estructura del molde: Diseñar la estructura del molde según la forma y tamaño del producto. Incluyendo el molde superior, el molde inferior, el núcleo del molde, la cavidad del molde y otras partes del molde. El diseño estructural del molde debe considerar la forma, el tamaño, el material y otros factores del producto, así como el método de apertura y cierre del molde, el sistema de enfriamiento, el sistema de escape, etc.
Determine el material del molde: seleccione el material del molde adecuado según los requisitos del producto y las condiciones de uso del molde. Los materiales de moldes más utilizados incluyen acero para herramientas, acero aleado, etc. La selección de materiales para moldes debe considerar la resistencia, dureza, resistencia al desgaste y otras propiedades del material.
Realizar diseño detallado del molde: Realizar diseño detallado del molde según el diseño estructural del molde. Incluyendo el tamaño, forma, tecnología de procesamiento, etc. de las piezas del molde. El diseño detallado del molde debe considerar factores como el montaje y la mantenibilidad del molde.
Fabricación y depuración del molde: después de completar el diseño del molde, es necesario llevar a cabo la fabricación y depuración del molde. La fabricación de moldes incluye la adquisición de materiales, el procesamiento, el tratamiento térmico y otros procesos. La depuración del molde incluye el montaje, ajuste y prueba del molde para garantizar que el molde pueda funcionar normalmente.
El diseño de moldes es un proceso complejo que requiere una consideración exhaustiva de los requisitos del producto, la estructura y los materiales del molde y otros factores. Un buen diseño de molde puede mejorar la calidad del producto y la eficiencia de producción y reducir los costos de producción. Por lo tanto, el diseño de moldes juega un papel importante en los procesos de desarrollo y fabricación de productos.
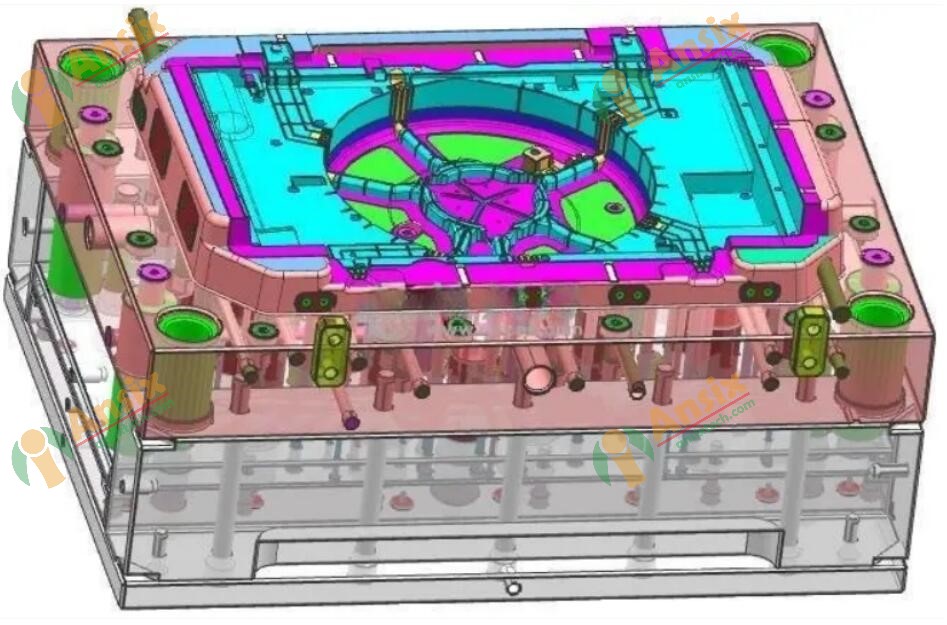
Fabricación de moldes y producción en masa.
La fabricación de moldes se refiere a la fabricación de moldes adecuados para la producción de productos mediante procesos como el procesamiento y el ensamblaje basados en dibujos y requisitos de diseño de moldes. El objetivo de la fabricación de moldes es lograr una producción de alta calidad, alta precisión y alta eficiencia.
Los principales pasos de la fabricación de moldes incluyen los siguientes aspectos:
Preparación del material: seleccione los materiales de molde adecuados según los requisitos de diseño del molde. Los materiales de moldes de uso común incluyen acero para herramientas, acero aleado, etc. La preparación del material incluye procesos como la adquisición, el corte y el procesamiento del material.
Procesamiento y fabricación: utilice equipos de procesamiento mecánico para procesar el molde de acuerdo con los dibujos de diseño del molde. Las técnicas de procesamiento incluyen fresado, taladrado, torneado, etc. El proceso de procesamiento requiere un control estricto de la precisión del tamaño y la forma para garantizar la calidad y precisión del molde.
Fabricación de piezas: los moldes suelen estar compuestos de varias piezas y es necesario fabricar cada una de ellas. La fabricación de piezas incluye procesamiento, tratamiento térmico, tratamiento de superficies y otros procesos. La fabricación de cada componente debe garantizar la precisión del tamaño y la forma para garantizar el montaje y el rendimiento del molde.
Ensamblaje y depuración: Después de completar la fabricación de cada componente, ensamble y depure el molde. El montaje del molde incluye el montaje, ajuste y fijación de piezas. Durante el proceso de depuración, es necesario verificar el movimiento y el funcionamiento del molde para garantizar que pueda funcionar normalmente.
Producción en masa: después de completar la fabricación y depuración del molde, el producto se puede producir en masa. Los moldes permiten fabricar grandes cantidades de productos de la misma forma y tamaño de forma rápida y precisa. El uso de moldes puede mejorar la eficiencia de la producción y la calidad del producto y reducir los costos de producción.
La fabricación de moldes y la producción en masa son procesos complejos que requieren una consideración integral del diseño del molde, los materiales, la tecnología de procesamiento y otros factores. Una buena fabricación de moldes puede mejorar la calidad del producto y la eficiencia de producción y reducir los costos de producción. Por lo tanto, la fabricación de moldes juega un papel importante en el proceso de desarrollo y fabricación del producto.